Sinopse: Componentes e equipamentos centelhantes de instrumentação, automação, telecomunicações e elétricos “Ex” podem ser fabricados com invólucros plásticos ou metálicos com o tipo de proteção Ex “d” (à prova de explosão), sendo adequados para instalação em áreas classificadas contendo gases inflamáveis Zona 1 ou Zona 2.
Equipamentos ou componentes com invólucros do tipo “à prova de explosão” (Ex “d”) são aqueles nos quais as partes internas centelhantes que podem causar a ignição de uma atmosfera explosiva de gases inflamáveis são confinadas no interior de um invólucro que é capaz de suportar a pressão desenvolvida durante uma explosão interna de uma mistura explosiva, e que também impede a propagação desta explosão interna para a atmosfera explosiva de gás externa, existente ao redor do equipamento Ex “d”, o que poderia ocasionar um acidente catastrófico nas instalações contendo áreas classificadas. No tipo de proteção Ex “d” as explosões não são evitadas, devendo consequentemente serem contidas.
Em 1921, o Departamento de Minas da Universidade de Sheffield, no Reino Unido, iniciou pesquisas sobre trabalhos com equipamentos “à prova de explosão”, em colaboração com o SMRB (Safety in Mines Research Board) e com a Associação Britânica de Pesquisas da Indústria Elétrica e Relacionada, mais tarde denominada ERA (Electrical Research Association). Em 1922 a Universidade de Sheffield, iniciou a execução de testes “comerciais” de equipamentos à prova de explosão para alguns fabricantes individuais, quando foi emitido o primeiro certificado por aquela Universidade.
O primeiro equipamento elétrico que foi utilizado em minas de carvão foi devido ao advento de motores com invólucros metálicos do tipo “à prova de explosão”, para acionamento de elevadores, ventiladores e equipamentos de mineração. Os operadores das minas de carvão observaram, porém, naquela época, que outros equipamentos elétricos, além dos motores, podiam ser também utilizados no interior de invólucros com paredes e juntas “reforçadas” do tipo “à prova de explosão”, como fusíveis, luminárias e tomadas.
No Brasil os equipamentos com invólucros metálicos do tipo “à prova de explosão” foram inicialmente utilizados na construção das primeiras refinarias de petróleo, a partir da década de 1930, com a instalação de uma primeira refinaria de petróleo no Rio Grande do Sul. Devido às influências do código norte americano de eletricidade (NEC) e das empresas de projeto e de montagem norte-americanas, criou-se no Brasil, a partir dos anos 1930 e 1940, nos fabricantes nacionais de equipamentos elétricos para áreas classificadas, uma “cultura” de utilização de equipamentos metálicos do tipo “à prova de explosão” com tampas flangeadas fixadas por meio de parafusos.
A figura seguir mostra uma vista interna de um invólucro Ex “d” com junta flangeada e tampa aparafusada (equipamento visto sem a tampa), no qual pode ser verificado o grande “volume interno vazio” existente no interior do equipamento. Pode ser verificada a grande quantidade de furos para fixação da tampa por meio de parafusos, necessários para suportar a pressão resultante de uma eventual explosão interna.
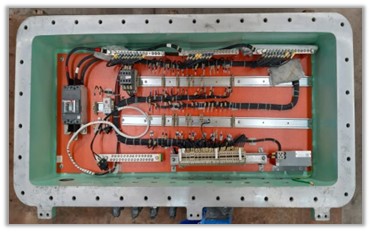
Vista interna de um invólucro metálico do tipo “à prova de explosão” (Ex “d”) com junta flangeada e tampa aparafusada fixada por meio de dezenas de parafusos (equipamento visto sem a tampa)
Os equipamentos elétricos e de instrumentação do tipo “à prova de explosão” necessitam possuir invólucros metálicos muito mais “reforçados” ou “robustos” do que os produtos elétricos ou de instrumentação para utilização “industrial comum”, a fim de suportar a pressão de uma explosão interna, sem se danificar e sem permitir que esta explosão interna seja propagada para o seu exterior. Uma luminária, por exemplo, que possua somente o tipo de proteção “à prova de explosão” para a fabricação de seu invólucro completo, apresenta um peso maior e procedimentos de montagem e manutenção “Ex” mais “complexos” quando comparada com uma luminária industrial “comum”.
Além disto, os requisitos de procedimentos de instalação, inspeção, manutenção e recuperação de uma luminária com invólucro metálico do tipo “à prova de explosão” são mais complexos e rigorosos, quando comparados com uma luminária industrial “comum” ou mesmo com uma luminária fabricada com outros tipos de proteção “Ex” combinados, como Ex “eb mb IIC” ou Ex “ec mc IIC”. O mesmo ocorre com outros tipos de equipamentos elétricos ou de instrumentação “Ex”, como por exemplo as caixas de terminais (Junction Box), que não possuem componentes centelhantes em seu interior.
Uma das características “conceituais” nestes tipos de invólucros metálicos do tipo “à prova de explosão” consiste na existência de grandes volumes internos vazios entre os dispositivos instalados em seu interior. Estes grandes “volumes vazios internos” permitem o acúmulo de grandes quantidades de atmosferas explosivas no interior do invólucro Ex “d”, provenientes, por exemplo, da região externa onde o equipamento se encontra instalado. Esta grande quantidade de atmosfera explosiva dá origem, por sua vez, a uma grande explosão no interior do invólucro, quando entra em contato com as partes centelhantes dos componentes que estão instalados no seu interior.
Esta grande pressão resultante da explosão interna, com geração de grande energia, necessita ser “contida” por meio de invólucros que possuam espessas paredes, caso contrário o invólucro seria destruído pela explosão interna. Além disto existe a necessidade de instalação de uma grande quantidade de parafusos para a fixação da tampa, caso contrário a tampa seria “arrancada” do invólucro ou permitiria a criação de “interstícios” que provocariam a propagação da explosão interna para o exterior do invólucro, colocando em risco toda a instalação de explosão. Por questões de segurança e de caso mais rigoroso de dimensionamento, os invólucros metálicos Ex “d” são ensaiados “vazios” nos laboratórios, fazendo com que o volume interno seja o maior possível, levando à necessidade de maiores espessuras de parede e de maior quantidade de parafusos de fixação das tampas.
Os próprios fabricantes de equipamentos com invólucros metálicos do tipo “à prova de explosão” com tampas flangeadas fixadas por diversos parafusos são preocupados com a segurança que estes equipamentos podem ou não proporcionar quando instalados em áreas classificadas e alertam os proprietários deste tipo de equipamento Ex “d” sobre as possibilidades de propagação das explosões primárias (que podem ocorrer no interior do invólucro Ex “d”) resultando em explosões secundárias (que podem ocorrer do lado de fora, ao redor do invólucro Ex “d”), com as possíveis consequências “devastadoras” que podem ocorrer, decorrentes destas indevidas propagações
De acordo com um dos maiores fabricantes mundiais de equipamentos “Ex” este tipo de situação de risco, que pode ocorrer nos casos em que apenas um único dos diversos parafusos de fixação das tampas nos invólucros Ex “d” estiver faltando ou indevidamente apertado, pode ser verificado no vídeo instrutivo “An important safety message from Eaton Crouse Hounds Business: Understanding explosion Nema 7 proof enclosures”, disponível em: https://www.youtube.com/watch?v=nccrAqNUPbs
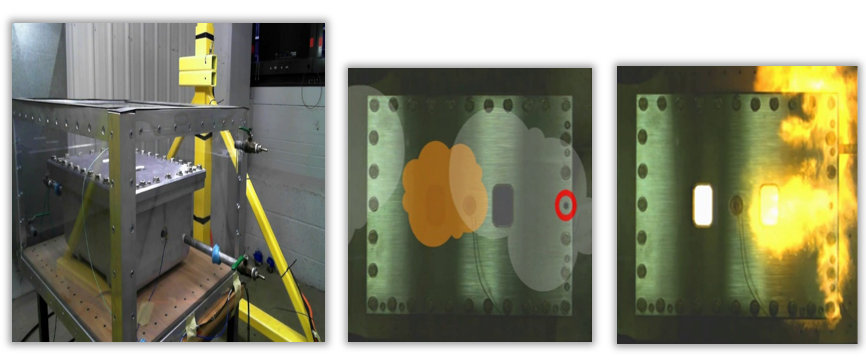
Vídeo didático produzido por fabricante de equipamentos “Ex” com invólucros metálicos Ex “d” mostrando as possíveis consequências catastróficas decorrentes da falta de um único parafuso de fixação da tampa
Outros problemas relacionados com os invólucros metálicos do tipo “à prova de explosão” com tampas flangeadas fixadas por diversos parafusos estão relacionados com a existência de danos mecânicos que podem ocorrer nas faces dos flanges que representam áreas de “passagem de chama”. Em casos em que estas faces flangeadas possam estar danificadas, causadas por exemplo por impactos mecânicos indevidos de ferramentas manuais, uma explosão interna pode ser indevidamente propagada para o lado externo do equipamento “à prova de explosão”, comprometendo a segurança das instalações em áreas classificadas, podendo causar efeitos “devastadores”, de acordo com o vídeo do referido fabricante de equipamentos “Ex” invólucros metálicos (flame proof ou explosion proof) Ex “d”.
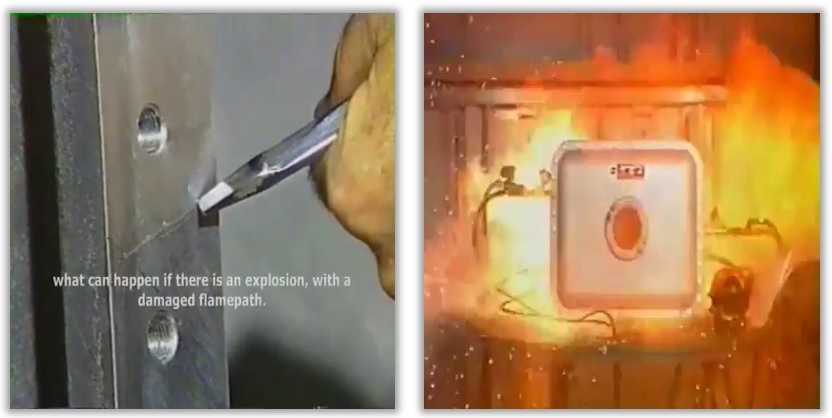
Vídeo didático produzido por fabricante de equipamentos “Ex” com invólucros metálicos Ex “d” mostrando as possíveis consequências “devastadoras” decorrentes de juntas metálicas flangeadas com indevidos danos mecânicos
Um vídeo didático sobre este assunto mostra as possíveis “consequências” de equipamentos com invólucros metálicos Ex “d” que apresentem juntas flangeadas indevidamente danificadas mecanicamente: https://www.youtube.com/watch?v=MTP1FGZFPKU
Componentes individualmente certificados com o tipo de proteção “à prova de explosão ”
Como alternativas técnicas de fabricação de equipamentos com tipo de proteção “Ex” para dispensar a necessidade de instalação de invólucros metálicos Ex “d” com juntas flangeadas e tampas aparafusadas pode ser citada a instalação de dispositivos centelhantes no interior de invólucros pressurizados (Tipo de proteção Ex “p”), como nos casos de painéis locais de controle instalados em áreas classificadas.
Existe também disponível no mercado, desde a década de 1990, componentes centelhantes instalados no interior de um invólucro plástico do tipo “à prova de explosão” (Ex “db”), com terminais de segurança aumentada (Ex “eb”), com proteções COMBINADAS Ex “db eb IIC” (U). Utilizando esta técnica de fabricação são reduzidos os espaços vazios disponíveis para serem ocupados por gases inflamáveis no interior do invólucro plástico, fazendo com que ele possa suportar a pressão de uma explosão interna, sem deixar que esta explosão se propague para o meio externo.
A Figura a seguir mostra uma vista em corte de um exemplo de componente centelhante (disjuntor) montado no interior de invólucro Ex “d” (à prova de explosão), com terminais e invólucro plástico com tipo de proteção Ex “e” (segurança aumentada). Marcação Ex de IIC Gb, com certificação com sufixo “U” (componente “Ex”).
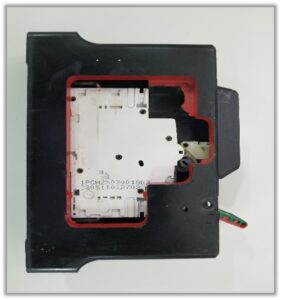
Vista em corte de um componente centelhante (disjuntor) montado no interior de invólucro plástico do tipo “à prova de explosão” (Ex “db”) e terminais do tipo “segurança aumentada” (Ex “eb”). Marcação do componente individualmente certificado: Ex db eb IIC Gb (U)
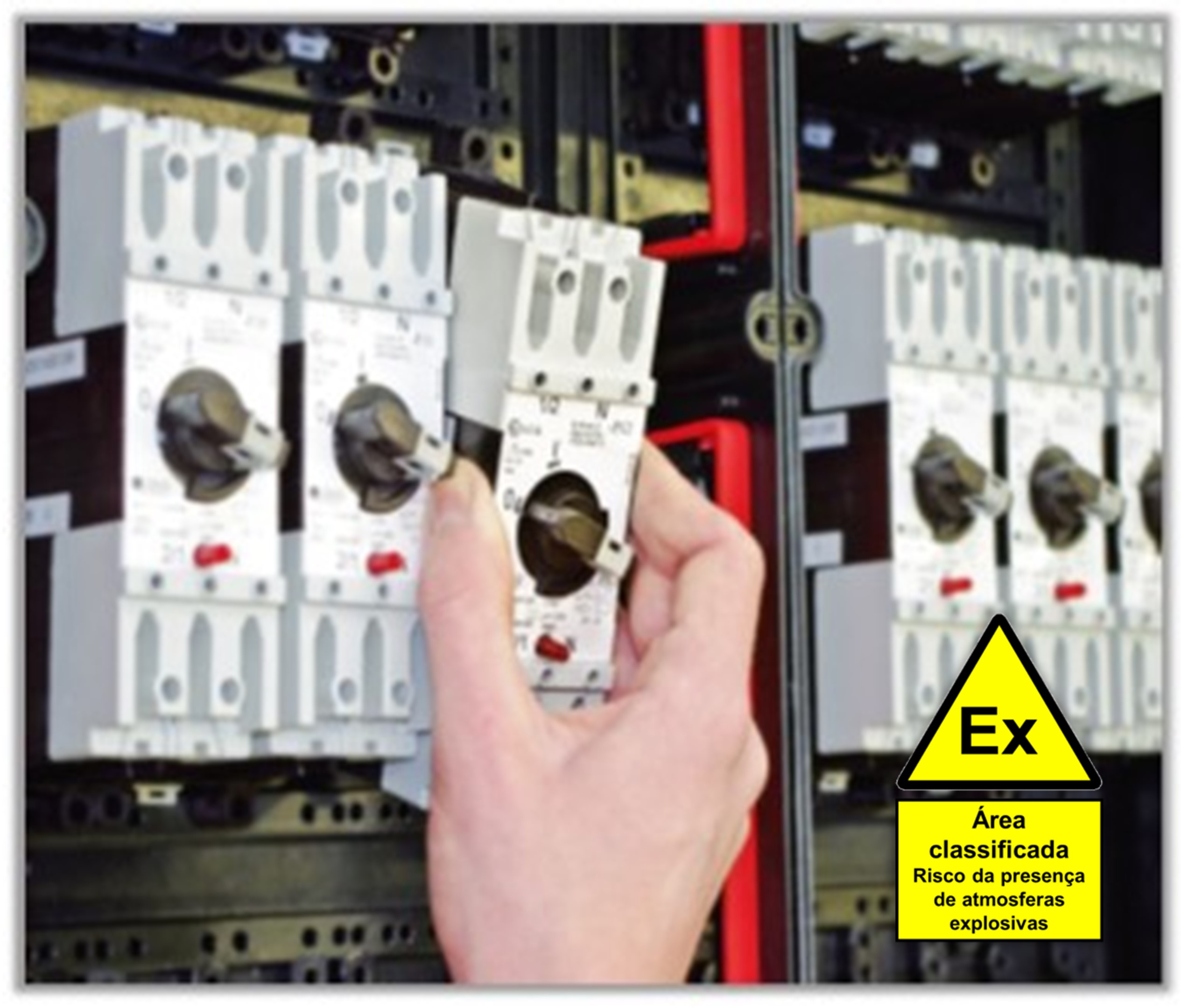
Exemplo de montagem em painel “Ex” para distribuição para circuitos de força contendo disjuntores tripolares com invólucros do tipo “à prova de explosão” (Ex “db”) fabricados em plástico, com terminais do tipo “segurança aumentada” (Ex “eb”).Marcação dos componentes individualmente certificados: Ex db eb IIC Gb (U)
Estes componentes Ex “db eb” podem ser instalados no interior de invólucros de segurança aumentada (Ex “e”), com invólucros externos em material termoplástico ou em alumínio ou chapas de aço inoxidável. Este tipo de componentes centelhantes Ex “db eb” IIC Gb (U) apresenta, dentre outros, os benefícios de dispensar a necessidade de um invólucro externo metálico do tipo “à prova de explosão”, dispensando também a necessidade de instalação de acessórios Ex “d” para eletrodutos, como por exemplo, unidades seladoras de eletroduto, niples e uniões macho/fêmea.
Estas combinações de tipo de proteções Ex db eb IIC Gb” (ou Ex “eb mb IIC Gb”) representam significativas soluções tecnológicas de mercado em termos de maiores facilidades de serviços de montagem, inspeção e manutenção “Ex” campo em áreas classificadas, contribuindo para reduzir a ocorrência de eventuais “desvios”, elevando os níveis de segurança em instalações de instrumentação, automação, telecomunicações e elétricas em atmosferas explosivas.
Podem ser citados como exemplos de equipamentos “Ex” que incorporam a combinação dos tipos de proteção “Ex” os painéis de controle e automação “Ex” as botoeiras locais de comando “Ex”, contendo componentes individualmente certificados com proteção combinada Ex “db eb” IIC Gb (U), nos quais as partes centelhantes de componentes elétricos (marcação tipo “U”), como botões de comando, contatos elétricos, chaves de controle, chaves seccionadoras de força, contatores, relés ou sinaleiros LED são individualmente “encapsulados” em pequenos invólucros plásticos do tipo “à prova de explosão” (Ex “db”), com terminais do tipo segurança aumentada (Ex “eb”).

Exemplo de montagem de painéis “Ex” para distribuição de circuitos de força e controle em áreas classificadas, com invólucros externos em aço inoxidável, contendo componentes centelhantes individualmente certificados com invólucros do tipo “à prova de explosão” (Ex “db”) e terminais do tipo “segurança aumentada” (Ex “eb”). Marcação completa do painel: Ex db eb IIC T4 Gb / Ex tb IIIC T135ºC Db
Continua na próxima edição
Por:
Roberval Bulgarelli
Consultor Técnico sobre equipamentos e instalações em atmosferas explosivasMestrado em proteção de sistemas elétricos de potência (POLI/USP) Membro de Comissões de Estudo do Subcomitê SCB 003:031 (Atmosferas explosivas) da ABNT/CB-003 (Eletricidade) Membro de Grupos de Trabalho do TC 31 (Atmosferas explosivas), TC 95 (Relés de proteção) e do IECEx (Sistemas internacionais de certificação “Ex”) da IEC
Organizador do Livro “O ciclo total de vida das instalações em atmosferas explosivas”