De acordo com a Norma Técnica Internacional IEC 60034-31 (Máquinas elétricas girantes – Parte 31: Seleção de motores energeticamente eficientes incluindo aplicações com rotação variável – Guia de aplicação), o custo de aquisição de um motor elétrico representa apenas cerca de 3% do seu custo total de operação, ao longo de sua vida útil. Os restantes 97% do custo se refere ao consumo de energia elétrica. Por este motivo, por questões de eficiência energética e de redução de custos de operação, é importante que os motores “Ex” possuam os maiores Índices de Eficiência (Código IE) possíveis.
Motores elétricos “Ex” frequentemente convertem cerca de 90% a 96% da sua energia elétrica de entrada em energia mecânica. Por isto, em função da grande quantidade de energia elétrica que estes motores consomem em todo o mundo, mesmo pequenas alterações em seus índices de eficiência podem representar grandes efeitos nos seus custos de operação. Existem, em diversos países do mundo, inclusive no Brasil, regulamentos que determinam o Índice de Eficiência energética mínimo (Códigos IE) a ser atendido pelos fabricantes de motores.
No âmbito internacional, a Norma IEC 60034-30-1 (Máquinas elétricas girantes – Parte 30-1: Classes de eficiência de motores c.a. alimentados pela rede – Códigos IE) estabelece os índices de eficiência energética internacionalmente consensados para motores elétricos (tais como IE3 ou IE4) pelos países participantes do TC-2 da IEC, do qual o Brasil é um país membro do tipo “P” (Participante). Sobre este tema relacionado com a eficiência energética de motores elétricos, o Sistema Internacional de Avaliação da Conformidade da IEC para Equipamentos Eletrotécnicos (IECEE) elaborou um Programa Global de Eficiência Energética de Motores (GMEE – Global Motor Energy Efficiency), como uma proposta de harmonização dos diversos programas existentes entre os diversos países.
Sob o aspecto de custos relacionados com os motores elétricos, deve ser ressaltado que mesmo uma única falha de um motor pode afetar adversamente a lucratividade de curto prazo de uma empresa, em função das possíveis paradas de produção e perdas por lucros cessantes. Falhas múltiplas ou repetitivas de motores podem até mesmo reduzir a competitividade de uma empresa, tanto em curto como em longo prazo. Por estes motivos, as empresas industriais necessitam de estratégias efetivas de gestão e de manutenção de forma a minimizar os custos gerais de compra e de operação de motores elétricos, além de evitar as paradas não programadas que são causadas pelas suas falhas não previstas.
Os serviços de reenrolamento de motores elétricos “Ex” representam uma atividade bastante frequente, em função dos elevados custos dos motores “Ex” de grande porte. Para estes motores, é economicamente viável a realização de serviços de reparos nos enrolamentos do estator e do rotor, ao invés da substituição do equipamento completo.
Pode ser verificado que, caso os serviços de reenrolamentos dos motores “Ex” sejam feitos de acordo com as “boas práticas de engenharia” existentes no mercado, a alteração da média da eficiência destes motores “Ex” fica dentro da faixa de precisão para os métodos de ensaio dos Índices de Eficiência – Códigos IE (da ordem de ± 0,2%), demonstrando que os motores “Ex” reparados ou reenrolados que seguiram tais boas práticas mantiveram seus Índices originais de Eficiência Energética.
No caso de ocorrência de falha destes motores “Ex” de alta tensão, em muitos casos existe a ocorrência de danos aos enrolamentos do estator, fazendo com que haja a necessidade de substituição destes enrolamentos. Nestes casos, a oficina de serviços de recuperação de equipamentos “Ex” deve obter do fabricante original do motor (OEM), se disponível, os dados de fabricação, isolamento e impregnação e montagem destes enrolamentos, de forma a assegurar que o motor “Ex” recuperado apresente as mesmas características de desempenho eletromecânico e térmico, em relação ao motor original.
Em muitos casos, na falta destas informações ou dados de fabricação, as oficinas de serviços de reparo de equipamentos “Ex” aplicam a tradicional técnica de “cópia de enrolamento”, mundialmente utilizada há décadas pelos usuários de motores “Ex” e pelas empresas de prestação de serviços de reparo e recuperação de motores. Esta técnica de cópia de enrolamento consiste em fabricar os novos enrolamentos substituintes, tendo como base a análise e a verificação dimensional dos enrolamentos existentes, reproduzindo as mesmas características de fios, espiras, formatos, materiais de isolamento, sistema de impregnação, montagem e amarração.
A Norma ABNT NBR IEC 60079-19 – Atmosferas explosivas – Parte 19: Reparo, revisão e recuperação de equipamentos “Ex” apresenta os requisitos aplicáveis à execução deste tipo de serviços de reenrolamentos de motores “Ex”, incluindo motores com tipo de proteção não centelhante – Ex “nA” e de segurança aumentada (Ex “eb” ou Ex “ec”), cuja proteção não depende de carcaças com invólucros especiais à prova de explosão ou pressurizados.
Para a execução dos serviços de remoção dos enrolamentos danificados do pacote do estator é aceitável o procedimento de diluição do verniz de impregnação das bobinas com solventes, antes da sua remoção, ou remoção a frio. O procedimento alternativo, que utiliza a aplicação de calor para facilitar a remoção dos enrolamentos, é aceitável, desde que esta operação seja realizada com cautela, com temperatura controlada no interior de um forno, de forma que não afete significativamente as propriedades magnéticas, as características de desempenho e o nível de isolamento entre as chapas magnéticas dos pacotes do estator e do rotor do motor.
A necessidade de cautelas especiais nestas circunstâncias deve-se ao fato de que um aumento nas perdas no núcleo do estator, que podem ser resultantes da perda das propriedades magnéticas das chapas de aço silício e da degradação do isolamento entre estas chapas, pode afetar significativamente os parâmetros do tipo de proteção “e” (tempo tE) ou resultar em que a temperatura de operação seja mais elevada em função das maiores perdas, fazendo com que classe de temperatura seja excedida, comprometendo a segurança do motor “Ex” após o reparo.
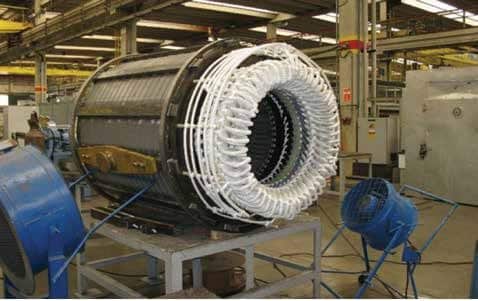
A oficina de serviços de recuperação de motores “Ex” deve certificar-se, em todos os procedimentos de recuperação, que após a conclusão dos serviços, os equipamentos estejam em perfeitas condições de operação e em conformidade com as normas técnicas aplicáveis para os tipos de proteção “Ex” do motor a ser reparado ou reenrolado. Sempre que aplicável, antes da inserção das espiras do estator nas suas ranhuras do núcleo, a integridade do isolamento interlaminar entre as chapas magnéticas do núcleo deve ser verificada, pela execução de ensaio de aplicação de fluxo, também denominado popularmente de “core-test” ou “loop-test”. O ensaio deve ser realizado pela indução, no núcleo do pacote do estator, de um fluxo magnético, com uma densidade mínima de 1,5 T (Tesla).
O ensaio deve ser realizado pela colocação de espiras através do pacote magnético do estator, de uma forma similar ao das espiras de um transformador. O fluxo magnético deve ser mantido continuamente por um período mínimo de 30 min, enquanto se realiza uma monitoração da temperatura atingida pelo pacote magnético do estator, por meio de uma câmera termográfica do tipo infravermelho. O critério de aceitação do ensaio é a não existência de pontos quentes no pacote magnético, com temperaturas acima de 5 ºC acima das temperaturas médias dos pontos adjacentes no pacote do estator.
Existe também a necessidade de que o sistema de isolamento do motor “Ex” a ser recuperado seja refeito com os mesmos materiais e componentes do motor “Ex” original, de forma a manter as características de transferência de calor entre o cobre e o aço do pacote do estator ou do rotor. No caso de bobinas de enrolamentos com espiras pré-formadas, a localização e a espessura dos blocos de amarração nas cabeças de bobinas devem ser replicadas na cópia do enrolamento, sendo importante que o espaço entre os lados da bobina nas cabeças da bobina seja mantido tão próximo como possível daquele do fabricante original do equipamento. A rigidez dos materiais da amarração deve ser equivalente ou melhor daqueles utilizados pelo fabricante original do equipamento.
O método de impregnação utilizado pelo fabricante original do equipamento (OEM – Original Equipment Manufacturer) do motor “Ex” deve ser avaliado, identificando se os enrolamentos foram impregnados por meio de imersão, impregnação por meio de vácuo e pressão (VPI – Vacuum Pressure Impregnation) ou gotejamento.
A cópia do enrolamento deve utilizar o mesmo processo e, caso isto não seja possível, deve utilizar um processo alternativo para atingir a mesma penetração e recobrimento da resina de impregnação nos enrolamentos.
O isolamento da ranhura para a terra, por exemplo, por meio de forro ou fita linear ou espessura da parede de bobinas com espiras pré-formadas deve ser medido e o material utilizado deve ser identificado. Muitas das máquinas de baixa tensão possuem forros ou fitas fabricadas de um material laminado, tipicamente Nomex e Mylar, normalmente como três camadas de Nomex / Mylar / Nomex e, quando possível, a espessura total do material e das camadas individuais devem ser mantidas.
A Norma ABNT NBR IEC 60079-19 especifica os requisitos para a execução dos serviços de reenrolamento de motores “Ex”, incluindo a referência à Folha de Decisão IECEx TAG 2013/006 – informações requeridas para assegurar que o motor “Ex” com cópia de enrolamento tenha um comportamento eletromecânico e térmico similar ao do motor “Ex” original.
O Setor Elétrico
Roberval Bulgarelli